Laureato in Ingegneria Civile presso l'Università degli Studi di Brescia. Nel 2006 entra in Azienda come ricercatore dove si occupa principalmente di calcestruzzi leggeri, calcestruzzi ad altissima prestazione, durabilità del calcestruzzo e materiali da riciclo. Attualmente è coordinatore dell’assistenza tecnica della Direzione Tecnologie e Qualità. È membro UNI e CEN e partecipa ad alcuni gruppi di lavoro sulle norme relative al calcestruzzo. È membro del CTE (Collegio dei tecnici della industrializzazione edilizia) e del FIB (The International Federation of Structural Concrete) all’interno del quale partecipa al Task Group 2.11 (Structures made by digital fabrication).
Il futuro delle strutture in calcestruzzo: verso resilienza e innovazione tecnologica
Prende spunto dal titolo della seconda edizione del fib Italy YMG Symposium of Concrete and Concrete Structures “The future of concrete structures: towards resilience and technological innovation”, tenutosi a Roma lo scorso novembre 2021, questo articolo il cui scopo è fare il punto sullo stato dell’arte della ricerca sul materiale principe dell’edilizia moderna, il calcestruzzo. Il Symposium della fib Italia Young Members Group, rivolto a giovani ingegneri, dottorandi e Post-Doc che lavorano nel settore del calcestruzzo e delle strutture in cemento armato, organizzato con il supporto del Collegio dei Tecnici della Industrializzazione Edilizia (CTE), dell’Associazione Italiana Calcestruzzo Armato e Precompresso (Aicap) e della Fédération International du Béton (fib), è stata un’occasione di confronto e scambio di idee tra giovani ricercatori e professionisti sul tema del futuro delle costruzioni in cemento armato.
L’associazione fib Italia Young (YMG), riconosciuta dalla fib e operante nel pieno supporto delle attività della fib, nasce nel 2008 al fine di creare un network per i giovani ingegneri che lavorano nel settore dell’edilizia per promuovere e divulgare la conoscenza riguardo il Model Code e i fib Bulletins tra giovani ingegneri, studenti e liberi professionisti e favorire lo scambio di idee e il networking in ambito nazionale e internazionale con i soci della fib Young International e dei fib Young Groups delle altre nazioni.
Il fib Italy Symposium, organizzato con cadenza biennale, rappresenta il luogo ideale in cui creare un forum di dibattito sul futuro delle costruzioni in cemento armato. I lavori di ricerca e progettazione dei partecipanti, sottoposti a processo di revisione da parte di membri delle commissioni fib, vengono presentati e discussi davanti a un comitato scientifico composto da esponenti dell’industria e giovani accademici provenienti da differenti università italiane. Diversi gli argomenti e i temi oggetto delle ricerche e delle sessioni del Symposium, dai ponti ai tunnel, dalle strutture esistenti alle costruzioni prefabbricate, dal concetto di durabilità a quello di sostenibilità, dai ripristini e le riabilitazioni strutturali allo sviluppo di materiali alternativi per la riduzione della carbon footprint dei materiali cementizi, fino alla stampa 3D. Nell’ambito della “Digital fabrication & Sustainability” ho avuto il privilegio di presiedere come moderatore, insieme a Costantino Menna dell’Università di Napoli Federico II, la sessione dedicata alla progettazione e alle tecnologie digitali per le costruzioni e ai nuovi materiali a base cementizia per la stampa 3D.
Sostenibilità, innovazione tecnologica e resilienza
La sostenibilità, l’innovazione e la durabilità dei materiali da costruzione, al centro degli articoli e degli studi presentati nell’ambito delle sessioni in cui si è articolato il Symposium fib, sono i temi di grande attualità del mondo della ricerca e della produzione, nel quadro delle normative tecniche di settore. Un percorso virtuoso nella realizzazione di opere destinate a durare senza “violare” l’ambiente circostante non può infatti prescindere dai concetti di Ambiente, Innovazione e Durabilità. La sostenibilità e l’innovazione dei materiali edili sono le sfide del futuro, a cui devono dare risposta le aziende del settore. E in questa direzione vanno anche Italcementi e Calcestruzzi che fanno di questi temi la principale linea guida, studiando prodotti e soluzioni che riducono la CO2 e danno vita a un’economia circolare. L’attività in corso anche sulla frontiera del 3D Printing fa di HeidelbergCement Group uno degli interlocutori ideali della fib, in grado di offrire nuove opportunità di ricerca e sperimentazione su prodotti che si sposano con le nuove tecnologie del costruire, basati sulla combinazione dei tradizionali materiali per le costruzioni – come il cemento – con le nuove frontiere aperte dal digitale.
D’altra parte, la Global Cement and Concrete Association (GCCA), la più grande organizzazione al mondo di questo comparto che riunisce 40 dei produttori più grandi del pianeta e qualcosa come l’80% dell’industria con sede al di fuori della Cina, ha preso l’impegno di tagliare le emissioni di CO2 del 25% entro il decennio, puntando alla carbon neutrality entro la metà del secolo. L’industria del cemento sta promuovendo da diverso tempo l’economia circolare e la ricerca su sistemi di cattura e stoccaggio/utilizzo di CO2, per prodotti e processi a sempre minore impronta di carbonio. Due le date fondamentali: il 2030, quando dovrà essere raggiunta una riduzione del 55% rispetto al 1990, e il 2050, l’anno della neutralità carbonica. In vista del raggiungimento di questi obiettivi, l’impegno è quello di promuovere un’edificazione efficiente ed ecologica partendo dai materiali, preferendo calcestruzzi a basso impatto ambientale in termini di carbon footprint, embodied energy (energia grigia) e minor consumo di acqua e puntando sull’uso di calcestruzzi sostenibili, facendo in modo che le prestazioni dei materiali siano valutate già in fase di progettazione dell’edificio. Il calcestruzzo, infatti, è un materiale la cui sostenibilità può essere decisamente migliorata, agendo sul processo produttivo di alcune sue componenti per ridurre le emissioni di anidride carbonica rilasciate e optando per la sostituzione di parte delle materie prime usate, come ad esempio il clinker e gli aggregati, con costituenti sostenibili.
La nuova linea eco.build di Italcementi risponde a questo impegno con una gamma di prodotti a bassa impronta ambientale e con materie prime seconde provenienti da altri settori industriali e dal settore edile. L’azienda sostituisce con materiali di recupero le proprie materie prime naturali provenienti dalle attività estrattive (in cave e miniere) come calcare, argilla e scisti, utilizzando, fra i materiali alternativi, i rifiuti non pericolosi provenienti da altri settori industriali come le ceneri volanti, i gessi chimici, le scorie d’alto forno, e le scaglie di laminazione. Calcestruzzi, utilizza per i propri mix design materiali da riciclo – tutti sottoposti a rigidi tracciamenti – come aggregati per la produzione di calcestruzzo. Queste pratiche consentiranno una importante riduzione nell’utilizzo di risorse naturali aiutando così a contenere il riscaldamento globale, mantenendo sempre elevati standard qualitativi.
Ancora in tema di ecosostenibilità e ambiente, per tornare alle parole chiave del Symposium, l’impegno del gruppo è anche nella progettazione e realizzazione di pavimentazioni drenanti, in risposta a specifiche richieste dei progettisti in termini di aumento del drenaggio e riduzione del deflusso superficiale. La gestione delle acque è sempre più necessaria a fronte dei ripetuti fenomeni atmosferici repentini e violenti. i.idro DRAIN è un calcestruzzo progettato per garantire il rispetto del ciclo naturale dell’acqua e la capacità drenante anche in condizioni di precipitazioni estreme, garantendo al tempo stesso un aiuto nel mitigare l’isola di calore tramite una temperatura superficiale ridotta rispetto, ad esempio, all’asfalto di circa il 20% nelle giornate più calde.
Ma la sostenibilità ambientale passa soprattutto attraverso la capacità di rispondere alle sollecitazioni dei contesti ambientali, nel corso del tempo, presupponendo una lunga durata delle opere. I due concetti che nel campo delle costruzioni, nel corso degli ultimi anni, hanno portato a nuove e buone pratiche sono quello di prolungamento della vita utile, che implica la durabilità, correlato a quello di incremento prestazionale. Uno degli aspetti più importanti dell’ingegneria moderna, in tal senso, di cui si è ampiamente discusso in occasione del Symposium fib, è quello della rigenerazione delle strutture, dei ripristini strutturali e del retrofitting, con il quale è possibile portare l’elemento strutturale a un livello di sicurezza più elevato rispetto a quello del progetto originario. La possibilità di manutenere e valorizzare il patrimonio strutturale italiano con interventi necessari all’adeguamento alle normative vigenti delle strutture e, in particolare, all’adeguamento sismico è particolarmente significativa per le infrastrutture viarie, che devono garantire a cittadini e imprese la possibilità di muoversi sul territorio in modo sicuro, tramite l’utilizzo di infrastrutture resilienti, cioè capaci di mantenersi efficienti anche in presenza di eventi o in condizioni estreme. Una possibile soluzione per il miglioramento della sicurezza, per lo sviluppo dei trasporti sul territorio nazionale e per la riabilitazione delle opere d’arte stradali – viadotti, ponti, cavalcavia – in calcestruzzo armato, consiste nell’utilizzo di innovativi micro-calcestruzzi fibrorinforzati ad altissima prestazione (come i.power RIGENERA di Italcementi). L’applicazione di questo calcestruzzo innovativo è stata validata da Italcementi e Calcestruzzi in collaborazione con l’Università di Brescia e l’Università Federico II di Napoli.
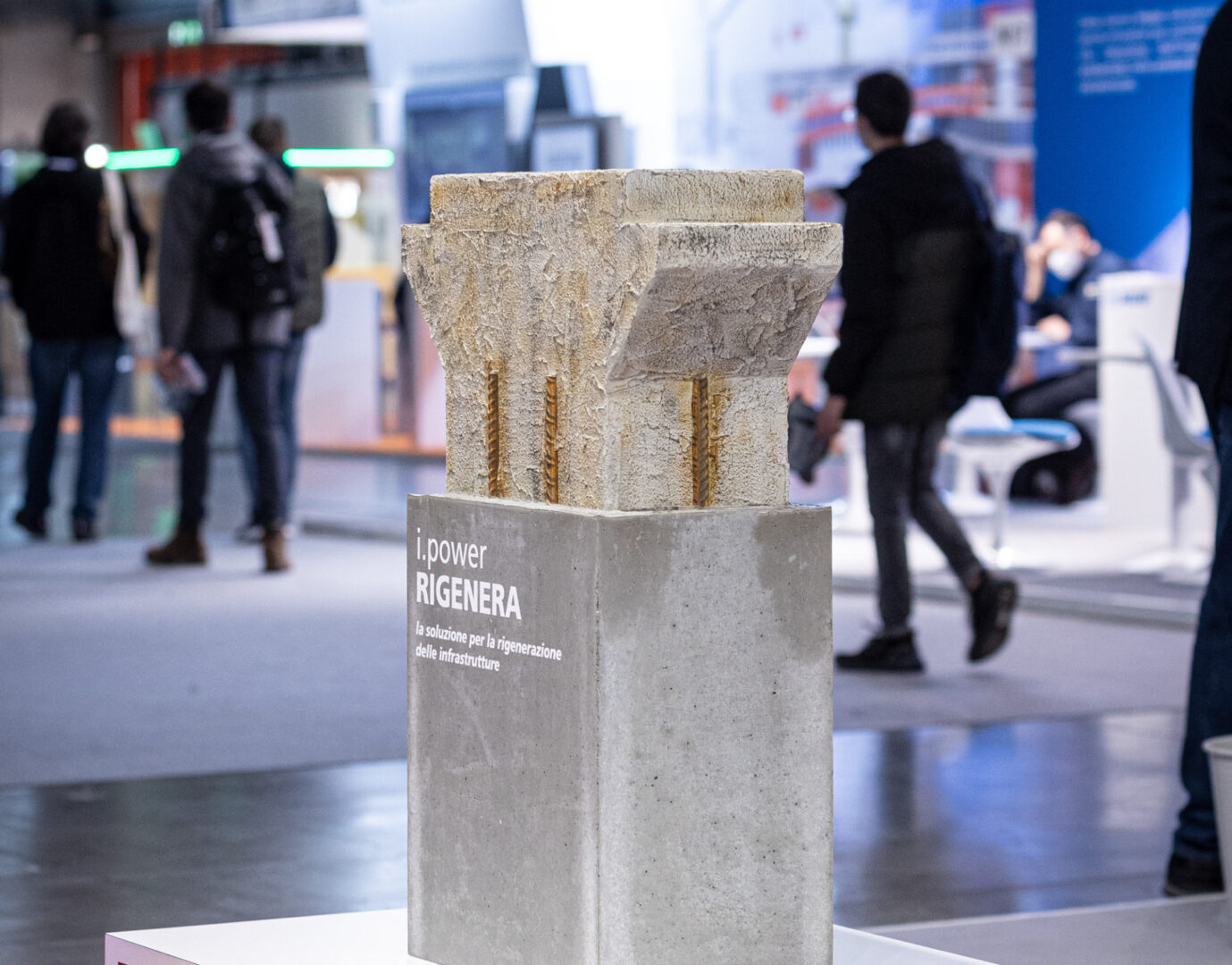
La soluzione per la rigenerazione delle infrastrutture
Quando una infrastruttura non è più adeguata alle caratteristiche di traffico e sicurezza sono principalmente due le soluzioni al problema: la costruzione di nuove infrastrutture che sostituiscano quelle precedenti, oppure il profondo adeguamento delle infrastrutture esistenti. Tuttavia, non sempre è possibile demolire, ad esempio, un viadotto sia per i costi elevati – demolire un viadotto può costare fino al 50% del valore costruttivo del nuovo – che per eventuali difficoltà operative. Adeguare una infrastruttura esistente, invece, permette di intervenire in modo efficiente (relativamente veloce), efficace (con costi contenuti), versatile (senza creare problemi alla viabilità) e sostenibile (evitando lo smaltimento dei materiali derivanti dalla demolizione dei vecchi manufatti). L’adeguamento è inteso sia come ripristino delle performance per cui le opere erano state progettate, sia come adeguamento ai nuovi carichi e alle normative sismiche introdotte negli ultimi 30 anni. Questi, sostanzialmente, i temi al centro della sessione dedicata alla rigenerazione delle strutture e delle infrastrutture.
La proposta messa a punto da Italcementi e Calcestruzzi offre una soluzione per riabilitare e rigenerare gli elementi strutturali in calcestruzzo armato delle infrastrutture che hanno bisogno di manutenzione per fare fronte al degrado strutturale e dei materiali causati dall’invecchiamento delle opere e dall’aumento del traffico. Obiettivo del Gruppo, insieme ai progettisti, risolvere i problemi di durabilità e quindi incrementare la vita utile delle opere, garantendo l’adeguamento sismico e il ripristino delle parti ammalorate, tutto in un’unica soluzione.
i.power RIGENERA consiste nel getto in opera per colatura di un micro-calcestruzzo ad alta resistenza, auto-compattante e fibro-rinforzato, che letteralmente “avvolge” l’elemento strutturale, creando una nuova pelle dello spessore di pochi centimetri, con proprietà meccaniche e durabilità elevatissime. Le proprietà meccaniche del materiale consentono di incrementare la resistenza e la duttilità degli elementi strutturali e di adeguarli alle richieste normative attuali. Le caratteristiche di durabilità del materiale consentono di proteggere le strutture esistenti e di incrementarne la durata oltre la vita nominale di progetto garantendo l’adeguamento sismico e il ripristino delle parti ammalorate, tutto in un’unica soluzione. La sua elevata fluidità e le sue prestazioni meccaniche, in termini di sostenibilità, permettono di realizzare spessori di pochi centimetri. Il prodotto inoltre contiene oltre il 10% di materiale riciclato. Il confronto tra un elemento strutturale ripristinato con i.power RIGENERA e uno ripristinato con un calcestruzzo ordinario, evidenzia una riduzione dell’emissione di CO2 globale di circa il 40% nel primo caso. Questo è dovuto alla quantità di materiale impiegato, circa tre volte inferiore nel caso di RIGENERA. Attualmente, questi materiali costituiscono oggetto di studio anche per la realizzazione di elementi strutturali prefabbricati, tipo travi e pannelli.
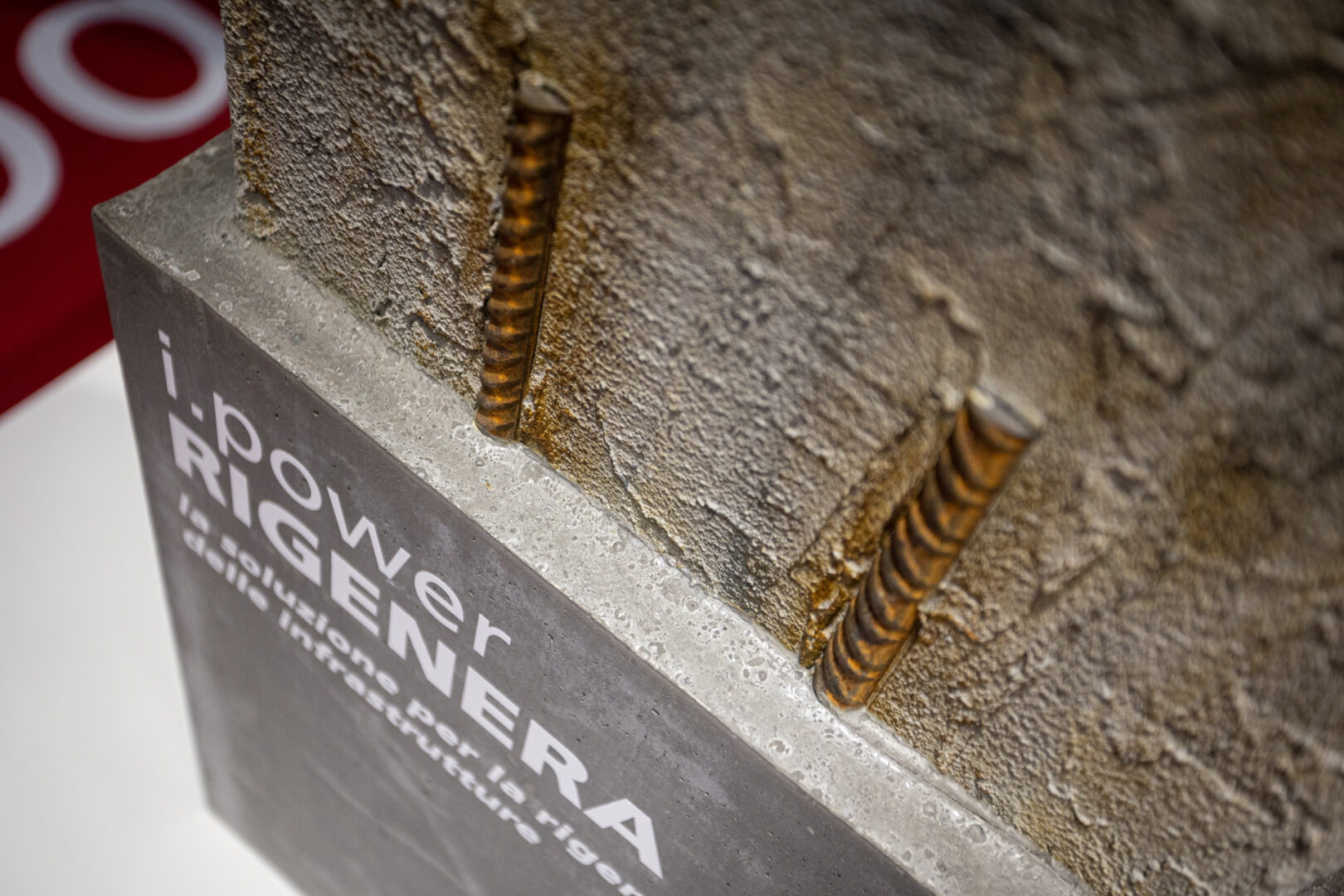
In termini di innovazione non si può non parlare di stampa 3D, tant’è che il Symposium della fib ha dedicato all’argomento una specifica sessione. Data la riconosciuta esperienza di Italcementi sul tema, gli organizzatori del simposio mi hanno contattato per presiedere in qualità di moderatore l’intera sessione. Fino a poco tempo, la tecnologia 3D Printing (3DP) è stata applicata utilizzando principalmente materiali come polimeri, metalli e argilla. I materiali cementizi sono in uso solo da pochi anni nel settore del 3D Printing. Questa tecnologia consiste nel depositare strati successivi di materiale sotto controllo computerizzato al fine di realizzare un modello progettato da uno specifico software 3D.
La crescente preoccupazione della società per la sostenibilità sta inducendo l’emergere di processi costruttivi innovativi per superare gli elevati impatti ambientali causati da quelli tradizionali. I processi di produzione additiva sono stati associati a un rapporto “costo-efficacia di fabbricazione” che riduce il consumo di energia, la domanda di risorse e le emissioni di CO2 durante il ciclo di vita del prodotto. La stampa 3D evidenzia un enorme potenziale nella produzione di geometrie complesse e nel ridurre il consumo di materiale attraverso l’ottimizzazione topologica, non possibile con le tecniche di costruzione tradizionali. Con il termine “ottimizzazione topologica” si intende uno studio che potrebbe consentire di progettare elementi strutturali più efficienti posizionando il materiale solo dove è strutturalmente necessario, ottenendo fino al 50% di risparmio di materiale rispetto a una costruzione convenzionale. Ciò significa che la valutazione delle prestazioni ambientali di elementi in calcestruzzo 3DP deve essere considerata, a parità di funzionalità, per tutta la loro vita utile, comprese le fasi di produzione, costruzione e demolizione. Tuttavia, la produzione e l’ottimizzazione di questi elementi complessi in calcestruzzo dipende dalle caratteristiche specifiche dei materiali, molto diversi dai calcestruzzi convenzionali. Essendo la 3DP una tecnologia senza casseforme, è necessaria una vera e propria ingegnerizzazione delle proprietà reologiche del calcestruzzo per garantire il mantenimento della forma e una conformità soddisfacente del materiale stampato rispetto alla forma progettata. Questo aspetto comporta indubbiamente un sostanziale vantaggio economico, dal momento che le casseforme rappresentano dal 28% fino alla metà del costo totale della struttura in calcestruzzo convenzionale. Inoltre, attraverso l’ottimizzazione topologica e l’utilizzo di fibre d’acciaio, è possibile ottenere un rinforzo, con una riduzione o addirittura, in alcuni casi, l’eliminazione delle barre d’acciaio, con ulteriori risparmi sui costi. Infine, il 3DP può ridurre l’impatto del costo del lavoro, grazie alla sua maggiore produttività rispetto alle costruzioni convenzionali e può consentire la realizzazione di un manufatto in qualsiasi area geografica, anche dove non si riuscirebbe ad arrivare con i mezzi tradizionali (betoniere).
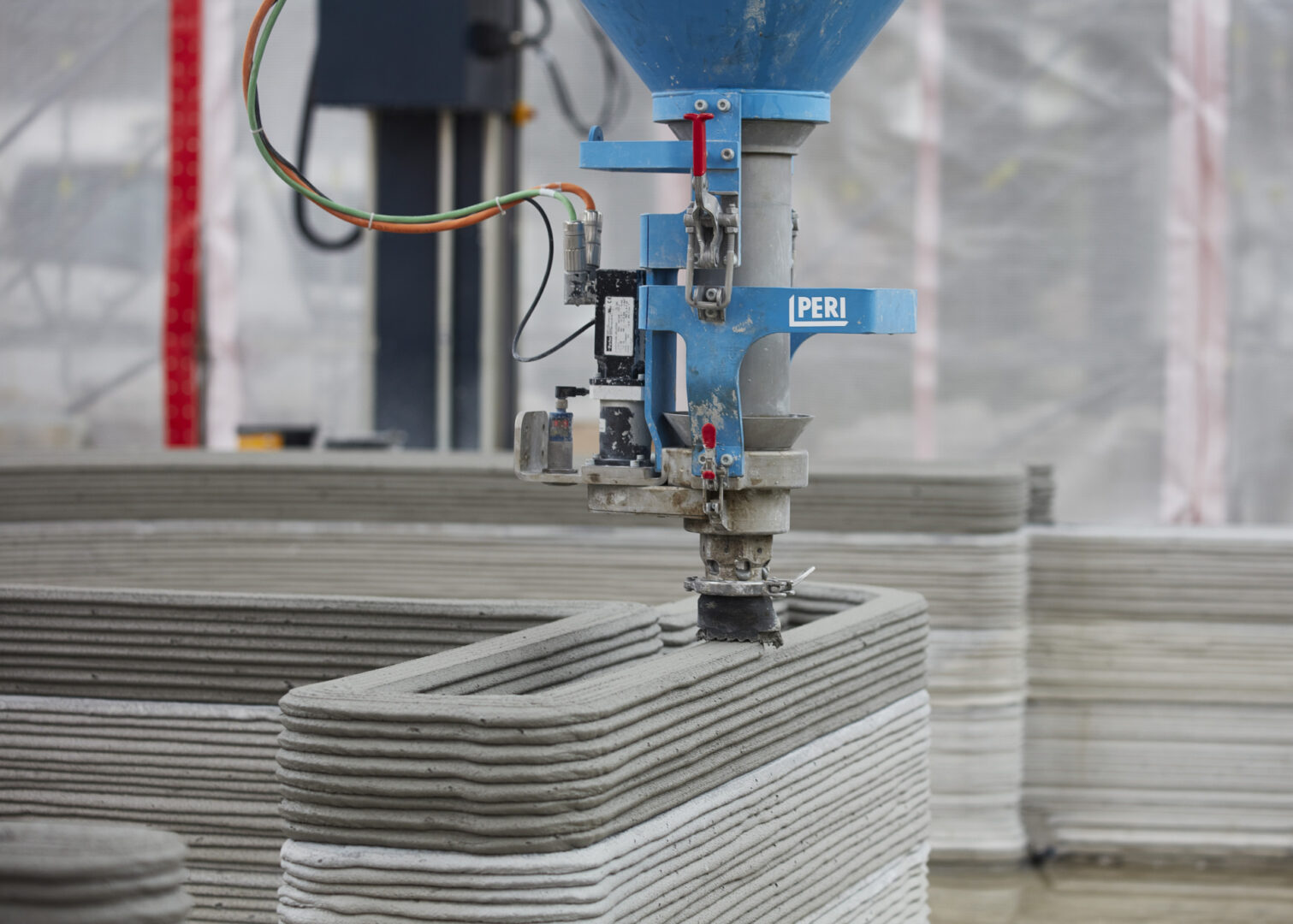
Al centro dei temi della sessione dedicata al 3D Printing, anche le tecnologie e i vantaggi che promettono di rivoluzionare il modo con cui componenti, strutturali e non, vengono prodotti. Altri vantaggi di cui si è discusso, sono legati all’automazione del processo produttivo, alla riduzione dei tempi e dei costi, alla riduzione del quantitativo di materiale adoperato e quindi alla maggiore sostenibilità economica ed ambientale associata della produzione degli stessi. Questioni ancora aperte che riscuotono grande interesse da parte di numerosi ricercatori che ne scorgono le grandi potenzialità. L’innovazione di Italcementi nel settore del cemento per il 3D printing, a partire dal 2015, anno in cui l’azienda ha cominciato a studiare la tecnologia di stampa 3D presso i laboratori di ricerca e innovazione a Bergamo, è stata una delle protagoniste della sessione.
Il formulato cementizio che è stato sviluppato, adattabile per le diverse tecnologie di stampa, possiede le caratteristiche necessarie per essere miscelato, pompato ed estruso attraverso ugelli, anche di forma differente, posti sulla testa di una macchina di stampa; al tempo stesso, è in grado di autosostenere il primo e i successivi strati depositati che, durante il processo di stampa, vengono posizionati uno sopra l’altro (stampa additiva). I laboratori di ricerca, che hanno sviluppato il know-how e le competenze tecniche, sono dotati di attrezzature e una stampante di dimensioni importanti con la quale si sono condotti studi sulla tecnologia, il processo e le formulazioni cementizie adatte per la stampa 3D con tecnologia di estrusione.
Il progetto “3D Housing 05” rappresenta la prima validazione in scala reale in cui Italcementi è stata protagonista. Questo progetto ha messo insieme le competenze e le società necessarie per realizzare la prima casa stampata in 3D in Italia. L’idea di casa stampata in 3D è stata presentata da Massimiliano Locatelli/CLS Architetti, ed è stata realizzata in collaborazione con Italcementi, Arup, Cybe Construction per la Milano Design Week 2018. Essa consisteva in una casa di 100 m2 in calcestruzzo stampato in 3D in opera in Piazza Cesare Beccaria. Successivamente, con questa tecnologia sono state affrontati e sono in corso di validazione anche altri sistemi costruttivi, quali i casseri per il settore delle costruzioni e i pannelli prefabbricati per le facciate.
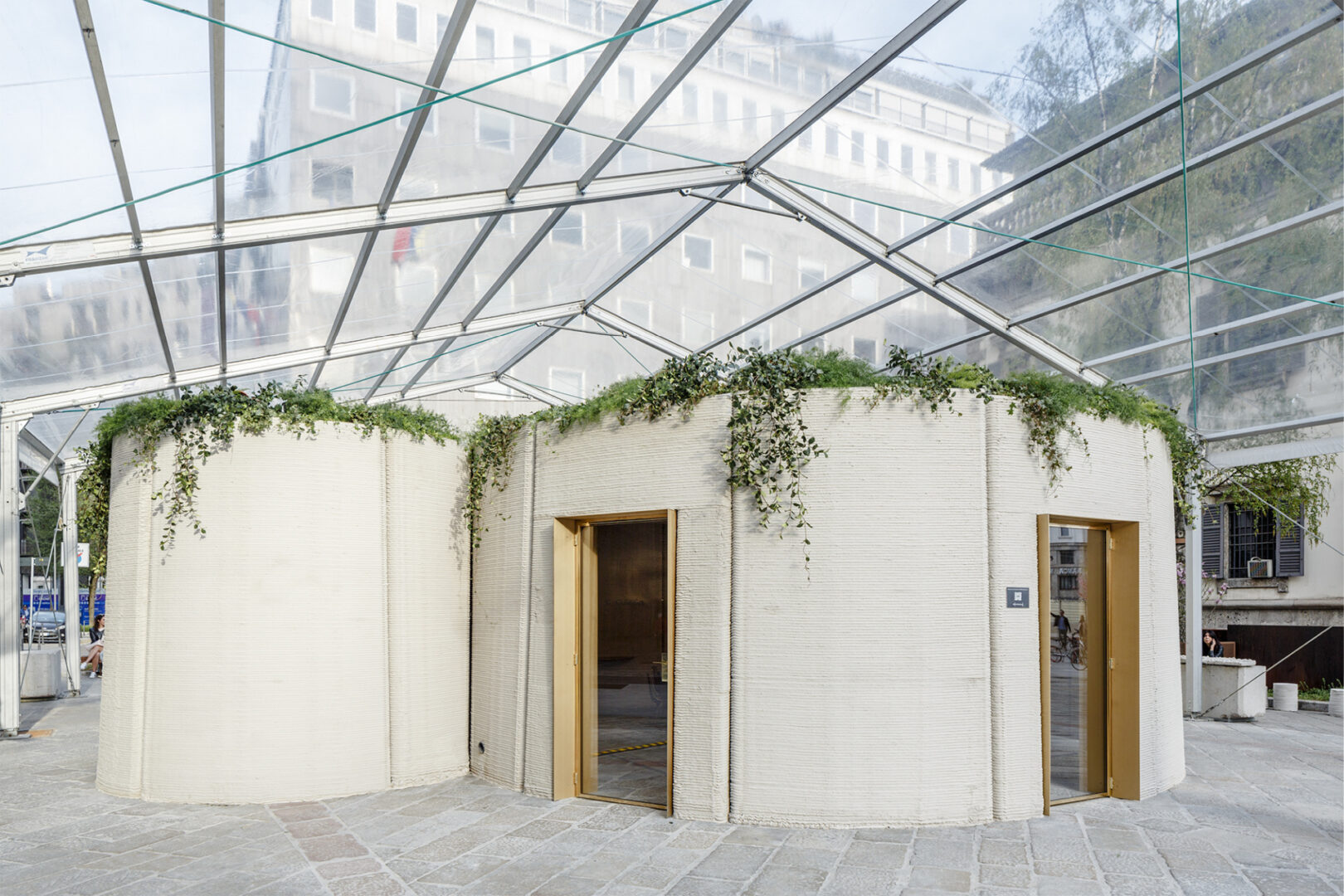
In Germania, invece, la prima casa stampata in 3D è stata realizzata nell’ottobre 2020, grazie al cemento frutto della ricerca italiana di Italcementi. Si tratta di una casa indipendente su due piani a Beckum, nella Renania Settentrionale-Vestfalia, di circa 80 m2 di superficie abitabile per piano e composta da pareti a tre strati riempite di mescola isolante. Il materiale ad alta tecnologia “i.tech 3D” è stato sviluppato nel centro ricerca di Italcementi a Bergamo, specificamente per la stampa 3D, ed è adatto per un uso versatile con diversi tipi di stampanti. La casa a Beckum è stata stampata da PERI, uno dei produttori principali di casseforme e di sistemi per impalcature nel settore delle costruzioni.
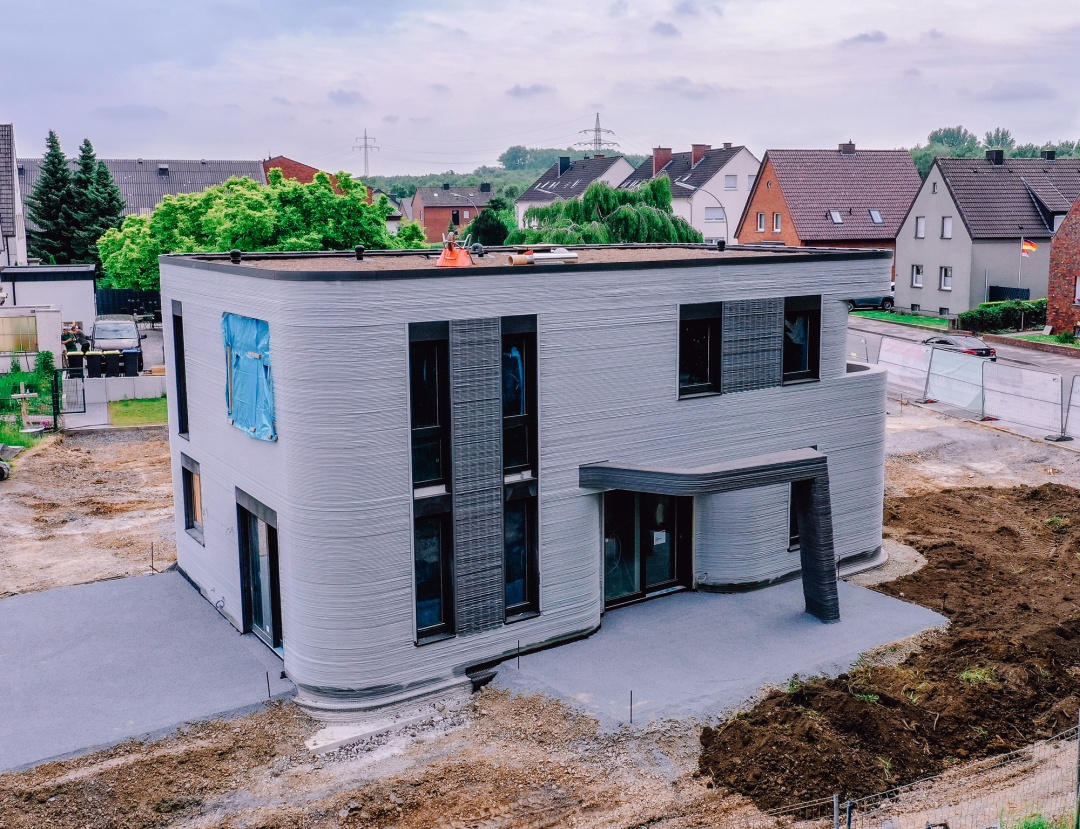
L’innovazione insieme a un aspetto oggi imprescindibile, l’attenzione per l’ambiente, sono i temi che più impegnano Italcementi e Calcestruzzi. La sostenibilità è oggi un valore strategico per il settore delle costruzioni e per questo è fondamentale poter contare sulle innovazioni della catena di fornitura e sul valore ambientale che prodotti, come il cemento, possono incorporare, perché ogni miglioramento tecnico volto alla riduzione della CO2 è un tassello importantissimo per il raggiungimento della sostenibilità del settore. Da 157 anni, Italcementi indirizza la sua ricerca nella produzione di materiali sostenibili con elevati standard qualitativi, che riducono l’emissione di CO2, favorendo l’economia circolare e rendendo sostenibile il mercato dei materiali per le costruzioni. Cementi e calcestruzzi altamente innovativi che rigenerino le infrastrutture e garantiscano la vita utile delle singole strutture, per cinquanta, cento, centocinquant’anni. Soluzioni nuove, in linea con la ricerca nazionale e internazionale e con l’ambizione del Gruppo di ridurre l’impronta ambientale dei propri prodotti e – di conseguenza – delle opere che con essi vengono realizzate. Le soluzioni costruttive ad alta sostenibilità saranno il vantaggio competitivo del futuro.