Laureato in Ingegneria Civile presso l'Università degli Studi di Brescia. Nel 2006 entra in Azienda come ricercatore dove si occupa principalmente di calcestruzzi leggeri, calcestruzzi ad altissima prestazione, durabilità del calcestruzzo e materiali da riciclo. Attualmente è coordinatore dell’assistenza tecnica della Direzione Tecnologie e Qualità. È membro UNI e CEN e partecipa ad alcuni gruppi di lavoro sulle norme relative al calcestruzzo. È membro del CTE (Collegio dei tecnici della industrializzazione edilizia) e del FIB (The International Federation of Structural Concrete) all’interno del quale partecipa al Task Group 2.11 (Structures made by digital fabrication).
I ponti in calcestruzzo: un patrimonio infrastrutturale da mettere in sicurezza
I crolli che hanno interessato il Ponte Morandi a Genova nel 2018 e altri ponti in calcestruzzo armato nel corso degli ultimi anni, sia in Italia che nel mondo, hanno portato una verità fondamentale sotto gli occhi di tutti: per poter continuare a garantire la loro funzione in sicurezza, le infrastrutture hanno bisogno di costante monitoraggio e manutenzione e, nel caso in cui si rendano necessari, di interventi di riabilitazione strutturale.
La vita di un ponte è legata a numerose variabili. Quando il crollo interessa un’infrastruttura costruita tra gli anni Cinquanta e Settanta, come per la maggior parte dei ponti in calcestruzzo armato crollati negli ultimi anni, i motivi sono da ricercare principalmente nel degrado naturale dei materiali che avviene durante la vita della struttura e nell’incremento dei carichi, che in alcuni casi possono superare la capacità portante prevista in fase di progettazione. Se a questi due fattori si aggiunge una maggior consapevolezza del rischio sismico, ora divenuto criterio di dimensionamento e verifica per le strutture di nuova costruzione, non è difficile immaginare come alcune infrastrutture attualmente in uso potrebbero non essere considerate sicure e rappresentare un rischio per la vita delle persone e il sistema dei collegamenti stradali in Italia. Per queste ragioni i ponti in calcestruzzo armato esistenti richiedono urgentemente una valutazione della loro sicurezza e un eventuale intervento di riabilitazione strutturale.
i.lab, il Centro Ricerca e Innovazione di Italcementi, ha sviluppato una soluzione in microcalcestruzzo fibrorinforzato ad altissime prestazioni (Ultra High Performance Fiber Reinforced Concrete – UHPFRC) per l’adeguamento strutturale e sismico dei ponti con un approccio all’insegna della rapidità e dell’economicità rispetto alla sostituzione dell’intera struttura. I costi legati all’interruzione del traffico stradale, alla demolizione del ponte ammalorato e alla costruzione del nuovo ponte, infatti, possono essere così elevati da rendere la sostituzione dell’infrastruttura preferibile solo in caso di gravissime carenze strutturali. La soluzione è presente oggi sul mercato con il nome di i.power RIGENERA, disponibile grazie alla rete commerciale di Calcestruzzi, la società di Italcementi che si occupa della produzione e della commercializzazione di calcestruzzo preconfezionato.
Rispetto ad altre soluzioni presenti sul mercato, il rivestimento con UHPFRC offre anche la possibilità di rinnovare la capacità dell’elemento di resistere alle azioni ambientali grazie all’elevata durabilità del nuovo materiale da riparazione. La tecnica di adeguamento consiste nell’esecuzione di strati sottili (fra 30 e 150 mm) di UHPFRC intorno (o sopra) elementi in calcestruzzo armato esistenti, come pile, travi o impalcati da ponte. Le operazioni di rinforzo non sono invasive e consentono, in molti casi, di non interrompere l’uso dell’infrastruttura (con notevoli vantaggi degli utenti). L’utilizzo delle armature può essere ottimizzato e le barre disposte solo nelle sezioni critiche dell’elemento, in quanto il materiale di riparazione è rinforzato con fibre. Grazie al rapido sviluppo della resistenza dell’UHPFRC e al ridotto utilizzo di barre di armatura, la durata delle operazioni di rinforzo può essere notevolmente ridotta, con benefici per la gestione della rete stradale.
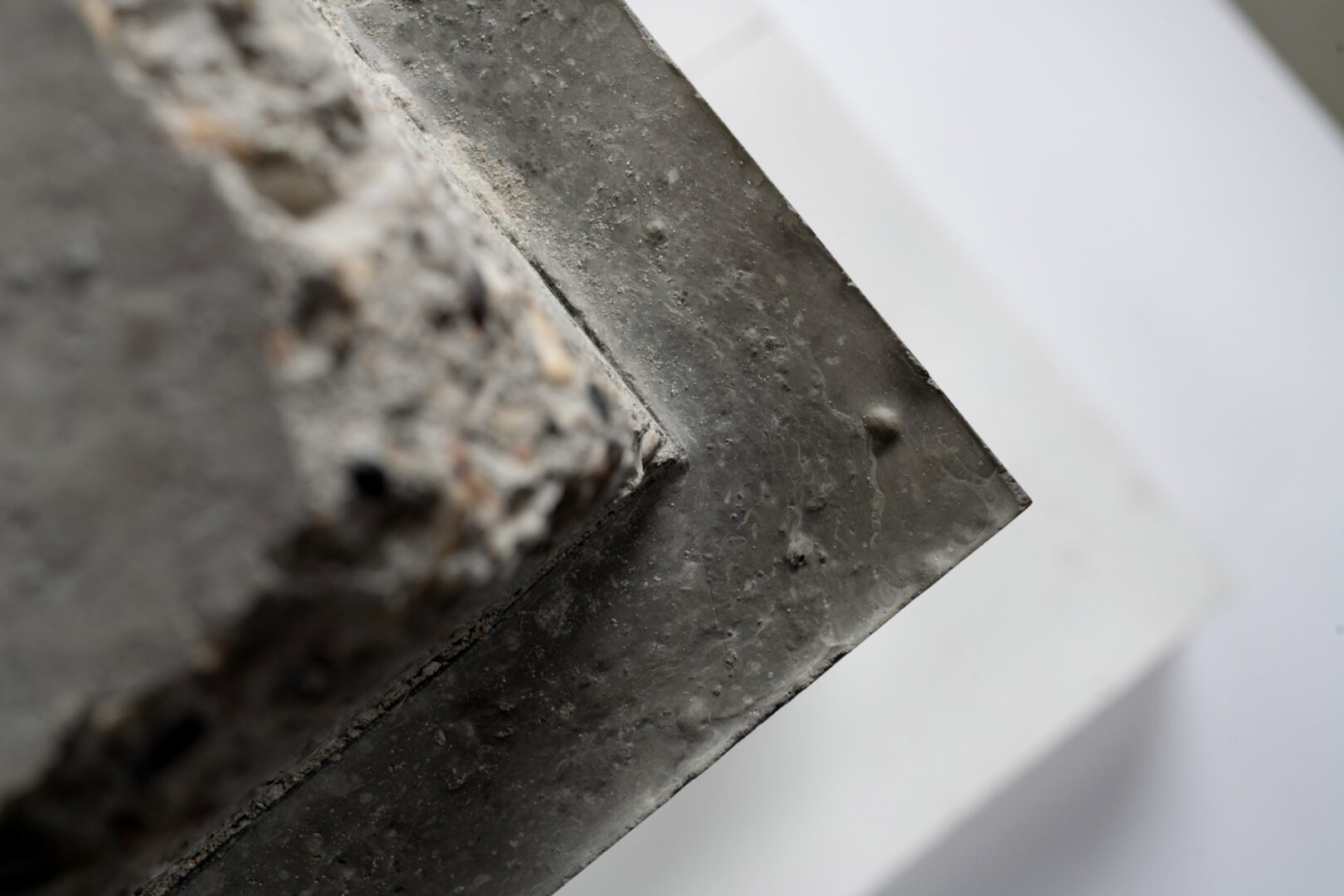
Prima della sua applicazione finale su una struttura in scala reale, l’UHPFRC è stato studiato a fondo per quanto riguarda le sue elevate prestazioni meccaniche, la sua interazione con il calcestruzzo ordinario e le sue elevate proprietà di durabilità. Presso l’Università degli Studi di Brescia e l’Università degli Studi di Napoli Federico II, è stata effettuata una serie di studi sulle applicazioni strutturali dell’UHPFRC. Inizialmente è stato studiato, sia sperimentalmente che numericamente, il rischio di fessurazione precoce dovute al ritiro vincolato delle pile da ponte rinforzate con UHPFRC. Questo problema è stato considerato in profondità in quanto i suoi effetti deleteri possono influenzare le prestazioni strutturali della struttura rinforzata e, soprattutto, la sua durata nel tempo. I risultati sperimentali hanno dimostrato lo sviluppo di sollecitazioni circonferenziali nel nuovo strato di riparazione a causa del ritiro vincolato dell’UHPFRC in condizioni controllate, misurato per mezzo di deformazioni circonferenziali con estensimetri incorporati nel getto. Il rinforzo costituito da fibre è risultato di fondamentale importanza per ottenere un rivestimento durevole. La presenza di fibre attenua lo sviluppo delle fessure e produce una distribuzione diffusa di microfratture (non visibili a occhio nudo e, dunque, meno problematiche per la durabilità) al posto di poche macro-fratture osservate su campioni senza fibre.
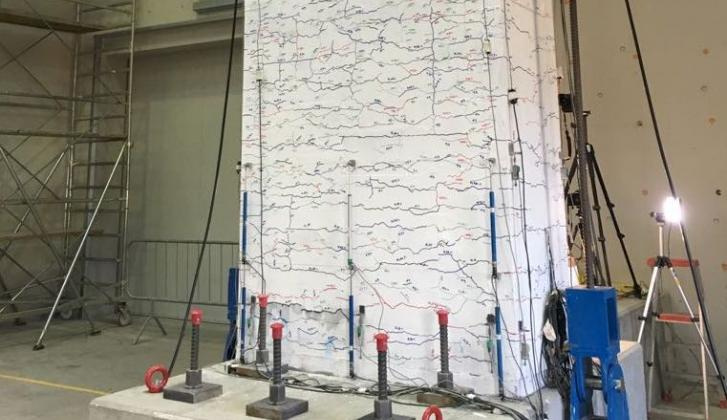
Infine, la tecnica di rinforzo è stata studiata sperimentalmente per mezzo di un campione di laboratorio di una pila da ponte allo scopo di valutare sperimentalmente la risposta sismica dell’elemento rinforzato mediante una prova di carico ciclico, simulando l’azione indotta da un terremoto. Il campione è stato testato sotto un carico verticale costante di 1000 kN con carico ciclico orizzontale variabile secondo un protocollo di prova basato su spostamenti laterali crescenti. Il rivestimento UHPFRC ha migliorato la risposta sismica allo Stato Limite Ultimo aumentando il carico laterale (sismico) di oltre il 70% rispetto all’elemento non rinforzato. La camicia in UHPFRC ha anche migliorato il comportamento strutturale allo Stato Limite di Esercizio determinando un quadro diffuso di microfratture con piccoli valori di ampiezza della fessura e, quindi, una minore facilità di penetrazione di sostanze aggressive all’interno della struttura.