Nato a Verbania nel 1959, è l’attuale amministratore della Società Fornari Srl. Diplomato geometra e con esperienza di alcuni anni universitari alla facoltà di Architettura, ha lavorato nel settore della pubblica amministrazione per circa undici anni. Nel 1994 insieme alla moglie Fiorella Fornari, figlia del fondatore, ha rilevato la Fornari Srl. Con lui lavora il figlio Samuele.
Prodotti belli, performanti e convenienti: la ricetta sostenibile di Fornari srl che convince progettisti e territorio
Lavoriamo nel settore del prefabbricato da sessant’anni, realizziamo lastre per solai, copertine a misura in cemento armato ma soprattutto muri di contenimento, lastre e doppie lastre. L’impresa Fornari, infatti, è nata nel 1965 dall’iniziativa di Maggiorino Fornari che da cottimista decise di mettersi in proprio facendo la presagomatura del ferro per cemento armato. La nostra sede è a Bieno S. Bernardino Verbano (VB).
Assecondando quella che era allora la direzione del settore delle costruzioni, dopo il boom edilizio degli anni Sessanta, l’azienda si era vocata alla prefabbricazione leggera e, quando nel 1995 l’abbiamo rilevata, come seconda generazione abbiamo iniziato a focalizzarci sul rapporto con i progettisti arrivando oggi a realizzare prodotti estremamente personalizzati. A questo proposito diciamo sempre che il nostro catalogo è fatto dalle idee dei clienti e dei progettisti con cui ci relazioniamo. L’abilità che abbiamo acquisito nell’organizzare la struttura metallica che funge da chassis nelle lastre in cemento armato ci permette di sviluppare le geometrie più diverse, con forme e altezze di ogni genere, per muri alti anche 8 metri.
Tra i manufatti che possiamo realizzare, la doppia lastra rappresenta certamente il nostro prodotto di punta. L’idea risale agli anni Novanta, quando il muro in cemento armato si costruiva ancora con i classici pannelli in legno dentro i quali si introduceva prima l’armatura in ferro e poi si gettava il cemento per procedere infine a disarmare togliendo la casseratura esterna e ottenere il muro in cemento armato. Fu in quel periodo che avemmo l’intuizione di creare un cassero che era già parte del muro. Essendo nati come presagomatori del tondo per cemento armato, con la sezione di saldatura all’interno dell’azienda, possedevamo la capacità di organizzare l’armatura interna e quindi decidemmo di provare. Così nacque la doppia lastra in cemento armato. I primi esemplari ebbero forme e altezze contenute ma questo limite lo abbiamo superato di slancio e la bilastra oggi è marcata CE e normata UNI (l’ente nazionale di unificazione delle norme in merito).
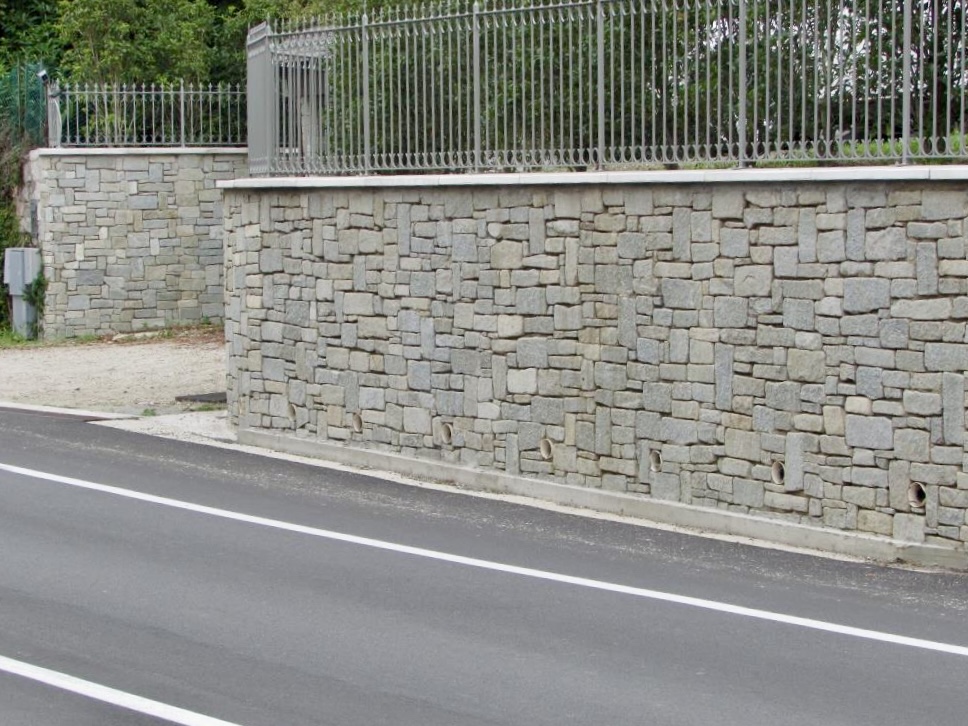
L’ulteriore sviluppo di questo progetto è arrivato intorno agli anni 2000, quando abbiamo iniziato a rivestirla con pietra naturale. L’occasione nacque dall’esigenza di un ingegnere della provincia di Novara che ci aveva richiesto una doppia lastra per rivestire un tornante in valle. Vivendo in una zona fortemente legata al settore lapideo, dove estraggono e lavorano la pietra naturale da sempre, ci venne l’idea di abbinare questa competenza presente sul territorio alla nostra nella prefabbricazione e proponemmo di consegnargli la doppia lastra già rivestita. Per realizzarla abbiamo industrializzato un’operazione che era cantieristica, lavorando su casseri in orizzontale e inglobando la pietra direttamente nel cemento al momento della produzione delle doppie lastre, prima della loro collocazione finale. Grazie a questa tecnica, più veloce ed economica della tradizionale, c’è un risparmio notevole sia per il committente che per l’impresa ma il vantaggio riguarda anche sicurezza e qualità. La doppia lastra, infatti, non prevede l’uso di ponteggi per l’istallazione e anche il problema del distaccamento dei materiali è stato risolto perfezionando la tecnica per annettere le pietre al calcestruzzo. I nostri muri reggono dopo dieci, quindici anni anche in condizioni di gelo ed intemperie.
Questa soluzione ci ha reso punto di riferimento per gli studi di progettazione di molte amministrazioni pubbliche che per ragioni ambientali e paesaggistiche, in determinate aree, devono seguire le prescrizioni regionali che prevedono il rivestimento in pietra naturale. Con questo prodotto noi siamo in grado di fornire una soluzione adatta e che fa risparmiare.
Abbiamo a catalogo circa 40 tipi di rivestimenti in pietra e disponiamo anche di un rivestimento, “Alpe Vecchio”, realizzato con pietre riciclate derivanti da demolizioni di baite e vecchi muri che puliamo e rigeneriamo. Il prodotto piace perché la pietra è informe e non di dimensioni standard come da cave moderne. È “super green” perché supera abbondantemente il 50% di materiali riciclati usati per la sua produzione e così rispecchia la nostra idea di sostenibilità, fatta di attenzione all’ambiente, alle persone, all’economia ma anche alla bellezza.
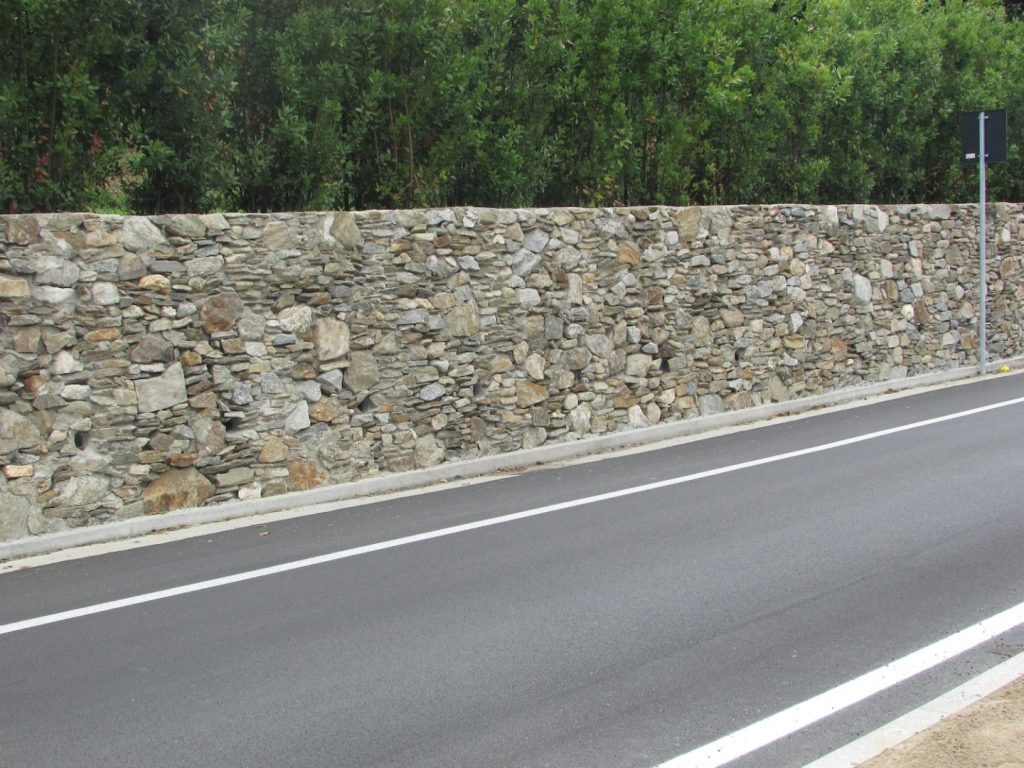
Tutti i nostri rivestimenti sono certificati CAM e da tre anni abbiamo in uso un cemento pozzolanico che si adatta anche alle esigenze dei cantieri marini, come quello che abbiamo attualmente a Genova, ma è più green del tradizionale perché richiede meno clinker. Avevamo iniziato testando il cemento di altoforno, ancora più sostenibile, ma il cemento di loppa non ci permetteva di scasserare in fretta per cui siamo passati al pozzolanico usando dei mix per accelerare la presa a breve termine e la resistenza ai solfati e all’acqua marina.
Siamo sempre alla ricerca di prodotti per rispettare e migliorare le normative in materia ambientale e per questo ci stiamo trovando bene con Heidelberg Materials Italia. La collaborazione con loro ci permette di confrontarci con un partner che ha i nostri stessi valori e che ci aiuta nelle scelte migliori per perseguire le nostre esigenze di sostenibilità. Abbiamo iniziato a lavorare con loro da cinque anni, quando eravamo alla ricerca di un cemento alternativo al Portland. Avevamo fatto già dei tentativi con diversi attori con cui però non riscontravamo costanza nella prestazione del cemento: un carico risultava magari ottimo e poi il successivo no. Con Heidelberg Materials abbiamo ottenuto invece questa continuità e, nonostante avremmo altri fornitori più vicini geograficamente, ci soddisfa e quindi non cambiamo. Riconosciamo Heidelberg Materials come un interlocutore con cui condividiamo il modo di vedere il lavoro, non in chiave meramente economica ma come un comportamento che implica una visione più ampia.
Come diceva un nostro cliente e amico che oggi non c’è più, l’Architetto Milesi dell’omonima impresa di Lugano: «Non dobbiamo pensare solo a risparmiare dei soldi ma prima di tutto a fare qualcosa che valga la pena di essere vista e vissuta». Con il suo studio di progettazione avevamo edificato a Morcote, in Svizzera, ormai due decenni fa, un autosilo da 1200 posti auto su 4 piani con più di 2.000 metri quadrati di muri, molto anche a vista, con un rivestimento fatto con masselli di Luserna cuneese di recupero. In quel momento il più grande cantiere del Canton Ticino. L’opera ci dette molta visibilità ma ci dimostrò anche che la qualità paga, permettendoti di lavorare sempre anche nei momenti che per altri sono di crisi, come questi. Molti colleghi oggi denunciano un calo di lavoro mentre noi abbiamo moltissime commesse con percentuali di aumento, solo sullo scorso anno, di oltre il 20-25%. A conferma di questo trend, in Italia vediamo moltiplicati i progettisti che già in fase di richiesta d’appalto chiedono certificazione CAM, prodotti che vanno verso quel risparmio energetico e ambientale di cui parliamo anche noi.
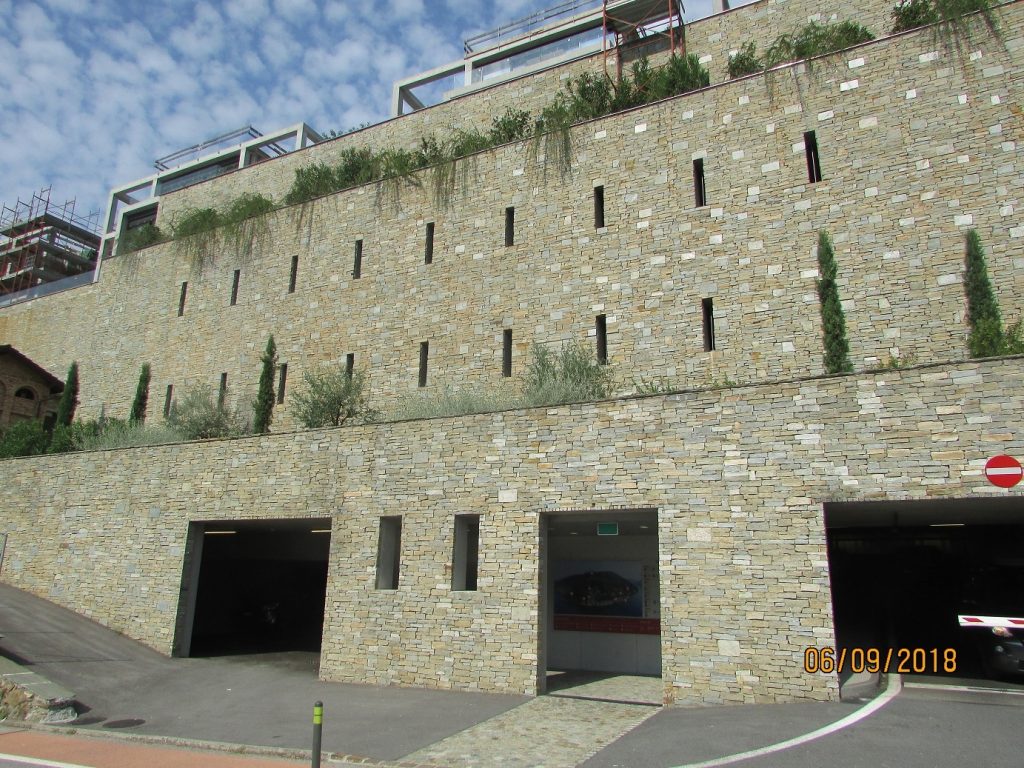
Quando abbiamo firmato il primo contratto con Heidelberg Materials è stato bello ritrovare questi valori anche nel loro codice etico. Come loro, noi crediamo che sostenibilità non possa e non debba essere solo quella economica ma passi attraverso le persone, che devono essere pagate il giusto e lavorare in un contesto piacevole, attraverso il rispetto dei clienti, che devono avere prodotti belli e di qualità, e quello dell’ambiente, per la cui salvaguardia siamo disposti a pagare un pò di più i prodotti che fanno davvero la differenza. Noi siamo convinti che se tutti facessimo qualcosa, ognuno nel nostro piccolo, tutto insieme diventerebbe tanto e grande. In Heidelberg Materials abbiamo riconosciuto questa stessa visione.
© RIPRODUZIONE RISERVATA