Laureata in Ingegneria Civile con un Dottorato di Ricerca in Meccanica delle Strutture, ha perfezionato i propri studi presso il dipartimento di Scienza delle Costruzioni dell’Università di Bologna e l’Imperial College di Londra, dove ha svolto attività di ricerca nel campo della dinamica delle strutture e della meccanica della frattura. Da diversi anni collabora regolarmente con le principali riviste tecniche di ingegneria e architettura, efficienza energetica e comfort abitativo, come autrice di articoli e approfondimenti tecnici. Instancabile viaggiatrice, attualmente risiede a Verona.
Dal ponte Genova San Giorgio un contributo fondamentale alla ricerca sui materiali e sulla tecnologia del calcestruzzo
Il 3 agosto 2020, a soli due anni dalla tragedia del Ponte Morandi, è stato inaugurato il nuovo viadotto sul Polcevera, realizzato da Webuild e Fincantieri, su progetto dell’arch. Renzo Piano. Genova San Giorgio, questo il nome del nuovo ponte, aperto al traffico il 4 agosto 2020. A un anno di distanza dall’inaugurazione del nuovo ponte, la ricerca e gli studi alla base delle scelte innovative sui materiali e sulla tecnologia del calcestruzzo impiegato nel “cantiere dell’eccellenza” proseguono all’insegna dell’ottimizzazione dei prodotti e del miglioramento della durabilità delle opere in calcestruzzo, coniugando sicurezza prestazionale, robustezza ed estetica, affidabilità e innovazione. Vale la pena, allora, riflettere con i protagonisti di tale ricerca sul reale significato del “modello Genova”, su cosa ha rappresentato per l’industria e la filiera delle costruzioni la ricostruzione del ponte e sul contributo fornito da questo cantiere alla ricerca sui materiali e sulle tecnologie, nel rispondere alle richieste della Committenza.
Una progettazione integrata e sistemica
Un cantiere, quello del ponte Genova San Giorgio, dove si sono intrecciate le migliori competenze dell’industria italiana delle costruzioni, con l’obiettivo di restituire alla città un collegamento essenziale per il suo tessuto sociale ed economico. Il cosiddetto “modello Genova”, impiegato nella ricostruzione del ponte, ha rappresentato non solo un’opportunità di riqualificazione di una parte della città di Genova, ma soprattutto un esempio positivo e virtuoso per l’Italia, un traguardo importantissimo tanto sul piano simbolico che infrastrutturale. Il successo del modello non deve essere solo ricondotto alla modifica del sistema normativo e al superamento dei vincoli procedurali attraverso la nomina di un commissario, dotato di poteri speciali e della facoltà di derogare alle normative, quanto piuttosto all’unità di intenti che ha visto tutti i soggetti coinvolti nel progetto lavorare nella stessa direzione, in via straordinaria, per la realizzazione nel minor tempo possibile di un’opera di così fondamentale importanza per il territorio.
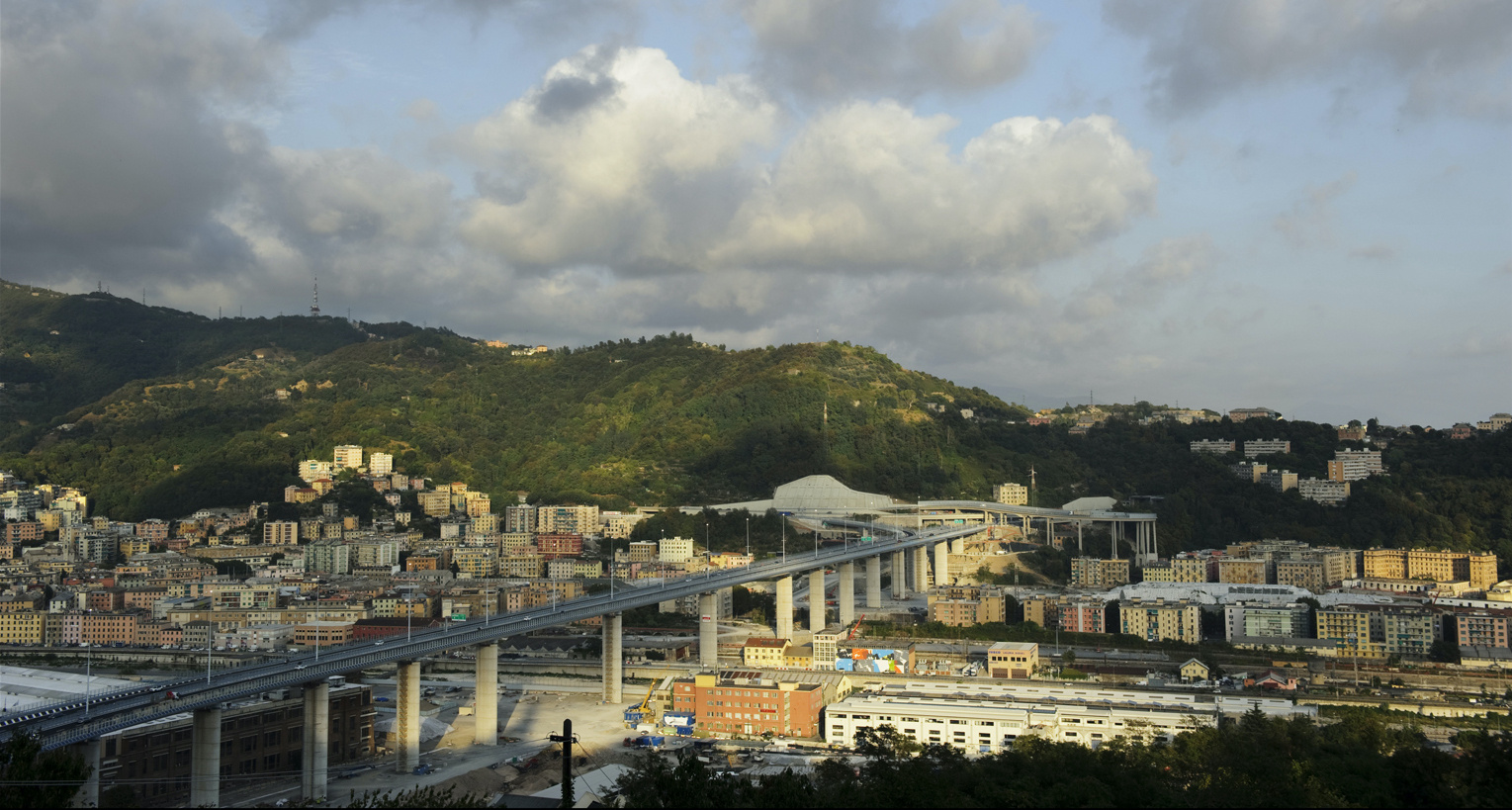
«La lezione più importante lasciataci dal cantiere del ponte Genova San Giorgio, a un anno di distanza dall’inaugurazione, è l’aver dimostrato che è possibile, per determinate opere di eccellenza, usare un approccio differente. L’unicità dell’opera, un concentrato di tecnologia, di qualità, di ricerca e di innovazione di prodotti e di processo, messo a punto per la prima volta in Italia, in tempi così brevi, è stata nell’approccio multidisciplinare del progetto e nella sinergia tra gli attori della ricostruzione. Fondamentale, infatti, è stata la collaborazione con la filiera. Una vision espressa e condivisa insieme alla committenza e a tutti i partner coinvolti nella realizzazione dell’opera, riconosciuti come interlocutori alla pari con i quali confrontarsi costantemente per la risoluzione delle varie problematiche del cantiere», afferma Andrea Zecchini, Head of Technologies and Technical Support, di Italcementi. «Questo Ponte rappresenta un nuovo modo di realizzare infrastrutture in Italia, grandi opere strategiche costruite in tempi giusti, con costi giusti e nel rispetto delle normative e della sicurezza».
Per i lavori di realizzazione degli elementi in calcestruzzo del ponte, pali di fondazione, plinti, piloni e soletta, Italcementi e Calcestruzzi, fornitrici dei materiali, hanno messo in campo una task force tecnologica che ha visto una “squadra” di tecnologi di tutta Italia e della Sede Centrale “passarsi il testimone” nell’affiancare i capi cantiere nel verificare e controllare la qualità della miscela fornita in qualsiasi momento. «Un lavoro incessante – prosegue Zecchini – per garantire assistenza tecnica ai quattro impianti della Calcestruzzi, società di Italcementi, negli stabilimenti di Chiaravagna, San Quirico, Polcevera e Genova Porto, impegnati nel confezionamento delle miscele per una fornitura di 67 mila metri cubi di calcestruzzo, pari a 160.000 tonnellate, che richiedeva, per il rispetto dei requisiti e delle tempistiche, l’assenza di problematiche di manutenzione o di impianto e il mantenimento di uno standard produttivo elevatissimo in termini di durabilità, rapidità, costanza delle performance reologiche in qualsiasi situazione atmosferica e assenza di difetti estetici». L’innovazione va ricercata anche nell’approccio tecnico adottato nella continua verifica dei prodotti e delle relative componenti, continuamente bilanciate, al fine di garantire costantemente, con tempi di realizzazione controllati, le prescrizioni di elevate performance richieste in termini di durabilità e sostenibilità dei materiali e per conseguire l’eccellenza anche nei tempi di realizzazione. «Un modello “100% certificato”, 8.000 controlli sul calcestruzzo e altrettante verifiche di taratura in impianto, test continui sul cemento per il mantenimento del livello cromatico, nell’ottica di mantenere costanti le performance del prodotto consegnato – conclude Zecchini –. Per Italcementi, il cemento non è solo materiale da costruzione capace di garantire performance e soluzioni, anche inedite, è ricerca, innovazione, competenze. Mantenere lo standard qualitativo in termini di omogeneità delle caratteristiche e performance di prodotto significa far sì che le maestranze, a valle, possano a loro volta conseguire sempre gli stessi standard produttivi».
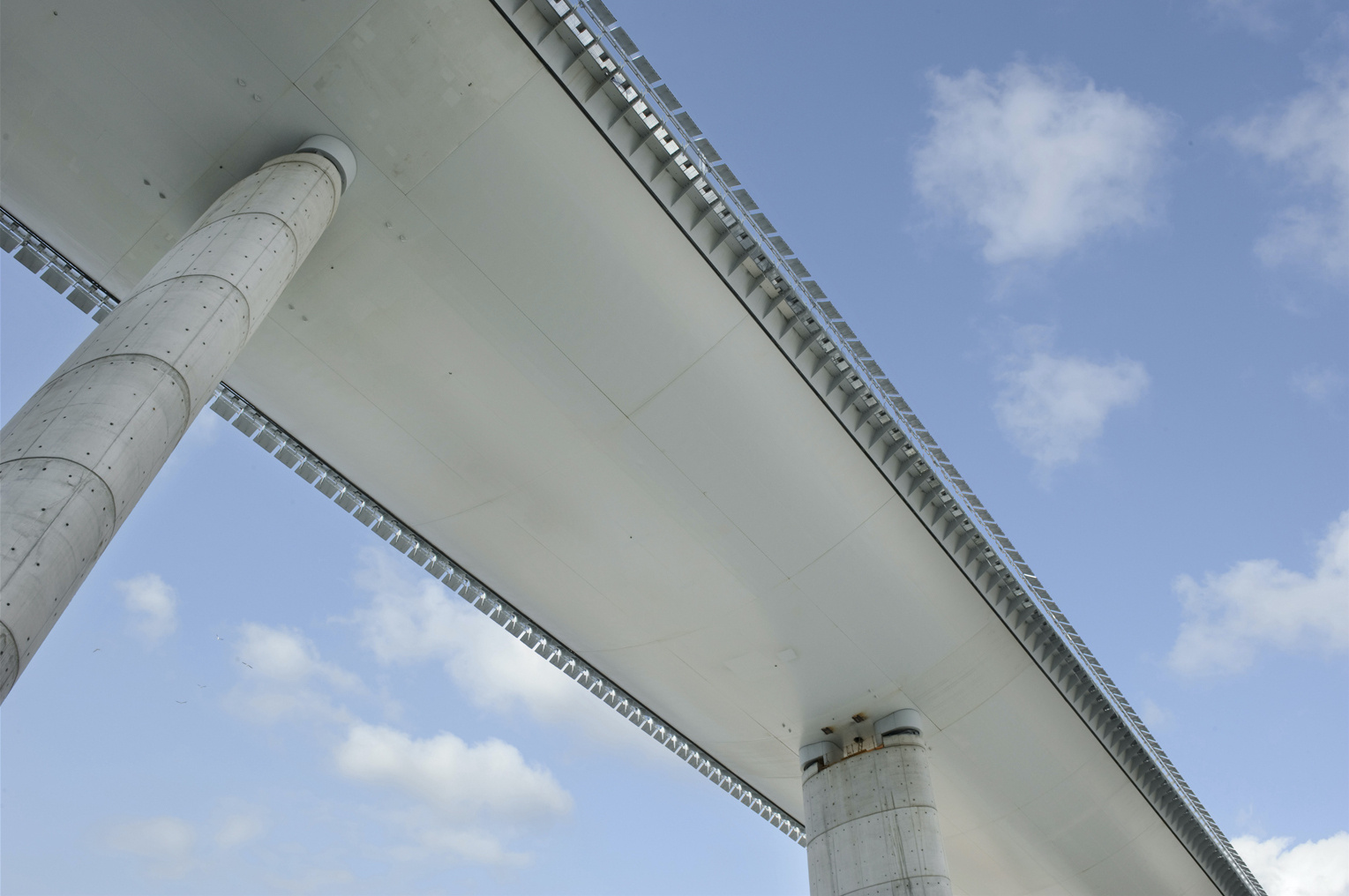
Il mix design del calcestruzzo
«Un ponte che sia come una nave, un grande vascello bianco che attraversa la valle, le cui pile diventeranno il materiale “urbano” del Parco della Val Polcevera e dovranno essere elementi “da abbracciare”, cioè belli da vedere e da toccare». Queste l’idea e la richiesta del progettista, in base alle quali è stato messo a punto il mix design del calcestruzzo, progettato per avere una elevata durabilità e caratteristiche costanti durante tutte le fasi del cantiere, senza tralasciare in nessun modo l’aspetto estetico e materico del materiale stesso. «In particolare le pile del ponte, che sono la parte più visibile dell’opera, hanno rappresentato l’elemento più sfidante per la messa a punto della miscela», spiega Francesco Santonicola, Responsabile del Laboratorio Centrale i.lab di Italcementi al Kilometro Rosso di Bergamo. «Per questi elementi – continua Santonicola – occorreva una miscela che garantisse, oltre ai requisiti prestazionali, un’adeguata lavorabilità e la costanza delle materie prime utilizzate nei vari impianti per il confezionamento di un prodotto in grado di soddisfare i requisiti cromatici del prodotto, costante per tutte le pile». La realizzazione mediante getti di calcestruzzo con l’utilizzo di casseri rampanti, poggianti sulla struttura stessa, richiedeva inoltre che al momento del getto il calcestruzzo di base avesse raggiunto la resistenza meccanica necessaria per sopportare il peso, oltre che del cassero, anche del nuovo getto. Pertanto, era necessario che lo sviluppo delle resistenze meccaniche avvenisse entro determinate tempistiche sia nel periodo estivo che invernale, in quanto il periodo di tempo intercorso per la realizzazione delle pile, compreso tra giugno 2019 e gennaio 2020, ha fatto sì che il calcestruzzo venisse posto in opera con un ventaglio di temperature molto diverse tra loro. «Questo – precisa Santonicola – perché la reazione di idratazione del cemento risente dell’abbassamento della temperatura e questo avrebbe influenzato la velocità di esecuzione dell’opera».
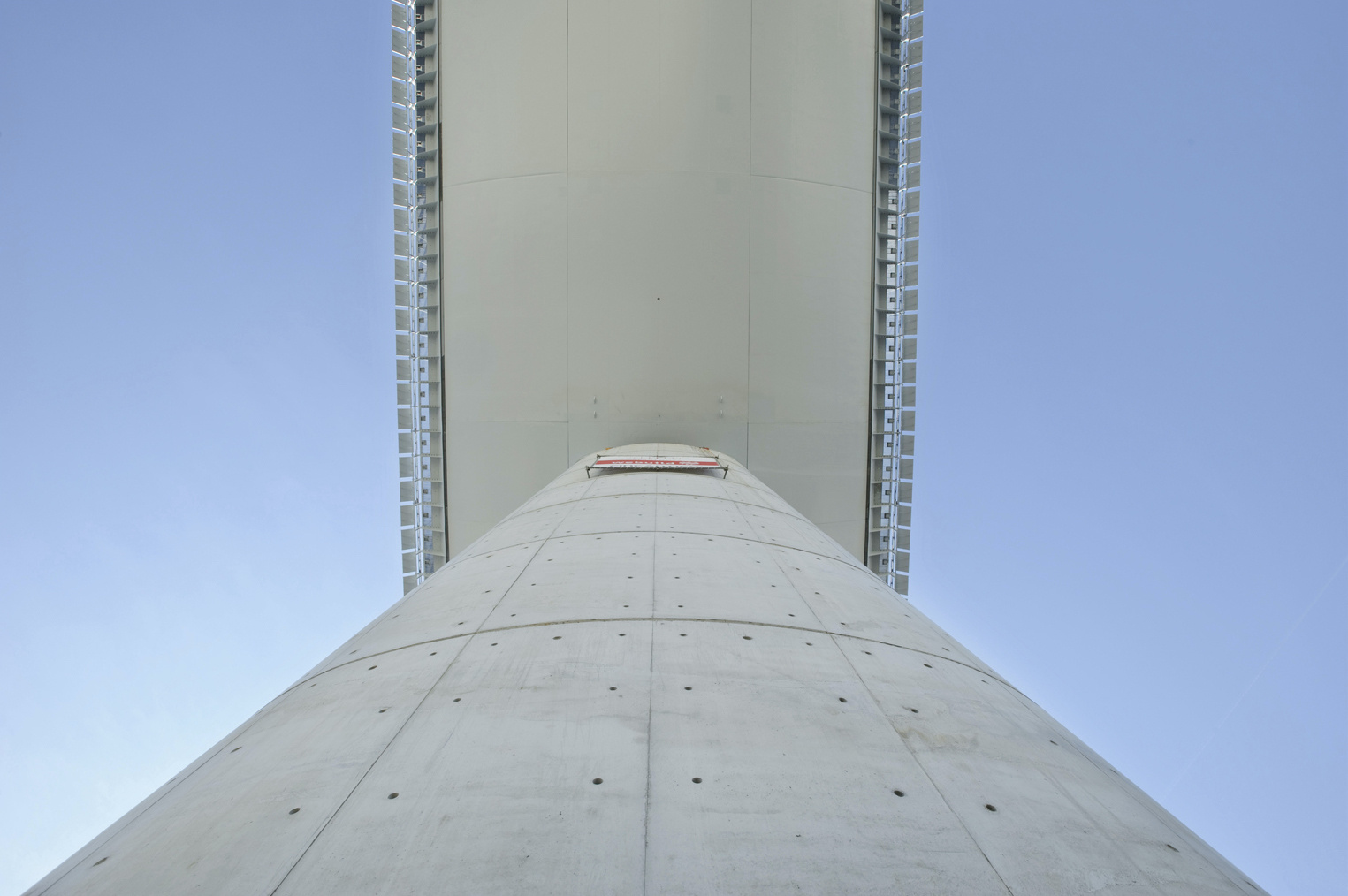
L’innovazione dei materiali
Per lo sviluppo degli additivi e del mix-design del calcestruzzo utilizzato per la costruzione delle pile del ponte al fine di garantire il rispetto delle esigenze strutturali, di durabilità e di sostenibilità ambientale dell’opera, la Direzione Tecnologie e Qualità di Italcementi si è avvalsa della collaborazione di Mapei e del CIRCe, Centro Interdipartimentale di Ricerca per lo Studio dei Materiali Cementizi e dei Leganti Idraulici dell’Università degli Studi di Padova, diretto dal prof. Gilberto Artioli.
Proprio per garantire che i tempi esecutivi della realizzazione delle pile fossero rispettati anche alle basse temperature, alla miscela è stato aggiunto un terzo additivo, sviluppato nei laboratori Mapei per accelerare l’idratazione del cemento e consentire lo sviluppo delle resistenze meccaniche in tempi più brevi.
«Questa tipologia di prodotti decisamente innovativi – spiega Giorgio Ferrari, R&D Group Leader, HPSS di Mapei – promuove e innesca, in modo istantaneo, la reazione di idratazione del cemento, di silicati idrati metallici e superfluidificanti policarbossilati (MeSH/PCE), grazie alle quali il conglomerato acquisisce una consistenza solida in tempi molto brevi». È un concetto nuovo rispetto agli acceleranti tradizionali, che operano secondo meccanismi diversi. «Questa diversità della microstruttura della pasta cementizia, – continua Ferrari – indagata anche nei mesi successivi alla posa delle pile del ponte e oggetto della nuova ricerca intrapresa con Italcementi, ha dimostrato che non solo si è riusciti a raggiungere il risultato primario, ovvero completare l’opera in tempi più brevi, ma anche a migliorare la microstruttura della pasta cementizia idratata, rendendola meno permeabile all’acqua e agli agenti aggressivi». Questo rappresenta un vantaggio importante ai fini della durabilità dell’opera perché, essendo il sistema più impermeabile all’acqua, migliora la resistenza alla penetrazione dei cloruri e alla carbonatazione del calcestruzzo. È importante sottolineare che migliorare la durabilità dell’opera significa anche conseguire una maggiore sicurezza per gli utenti nel tempo.
Dall’aggiunta degli additivi è derivata l’esigenza di approfondire come la nuova miscela ottenuta impattasse sullo sviluppo delle resistenze e su altri parametri fondanti legati all’aspetto della durabilità, a parità di resa estetica. «Sono stati effettuati – precisa Santonicola – ulteriori test di penetrazione all’acqua sotto pressione, di carbonatazione, di diffusione dello ione cloruro all’interno della matrice per indagare se questa fosse stata impattata positivamente, negativamente o fosse rimasta inalterata in termini di performance, a seguito della modifica». «Di fatto – continua Ferrari – la durabilità della pasta cementizia realizzata con l’additivo è migliorata rispetto alle caratteristiche del design di progetto. Risultato questo, di grande innovazione nella tecnologia del calcestruzzo e degno di grande attenzione, ottenuto grazie alla collaborazione decennale tra Mapei e il Centro CIRCe, finalizzata alla comprensione dei meccanismi di idratazione del cemento e allo sviluppo di nuovi additivi».
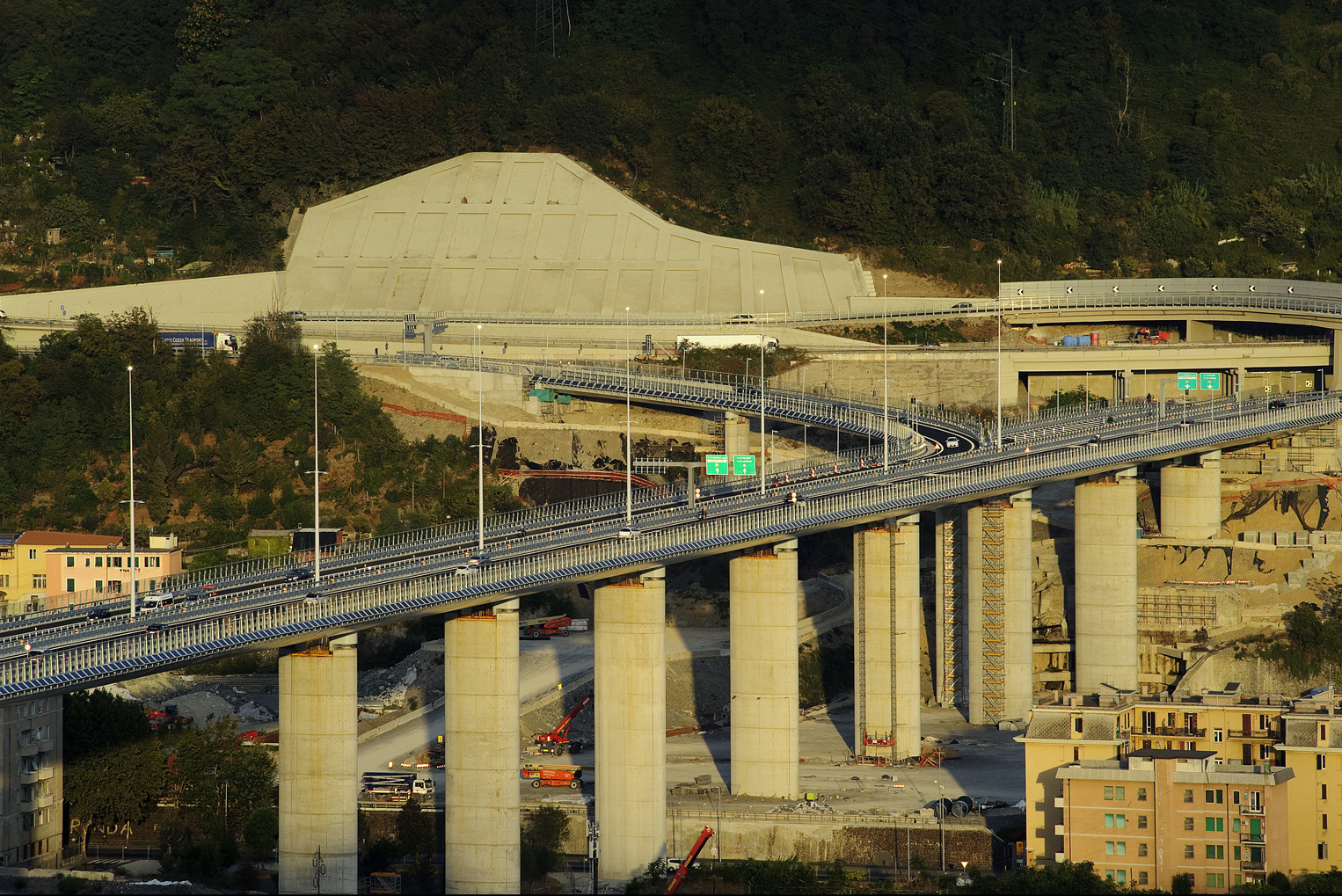
La collaborazione tra industria e università
Gli esiti delle prove e dei test effettuati sui meccanismi di interazione tra additivi e cemento utilizzati nel confezionamento del calcestruzzo impiegato per la realizzazione del nuovo ponte hanno confermato le aspettative di laboratorio e sono stati lo spunto per l’ulteriore sviluppo della ricerca, incentrata sul contributo di questa nuova generazione di additivi al miglioramento della durabilità delle opere in calcestruzzo. Alcuni risultati della ricerca saranno presentati al 2nd fib Italy YMG Symposium on Concrete and Concrete Structures che si terrà il prossimo novembre a Roma.
Un progetto che parte da lontano e che, nel 2018, ha avuto un riconoscimento con l’assegnazione della Medaglia Giacomo Levi da parte della Società di Chimica Italiana, Divisione di Chimica Industriale, per la collaborazione tra industria e università finalizzata allo sviluppo di prodotti industriali di rilevanza tecnologica. «La ricerca in atto – precisa Ferrari – può aprire una nuova pagina nel campo della tecnologia delle costruzioni; stiamo proseguendo le ricerche per comprendere a fondo le potenzialità di questo prodotto nell’interazione con la matrice cementizia».
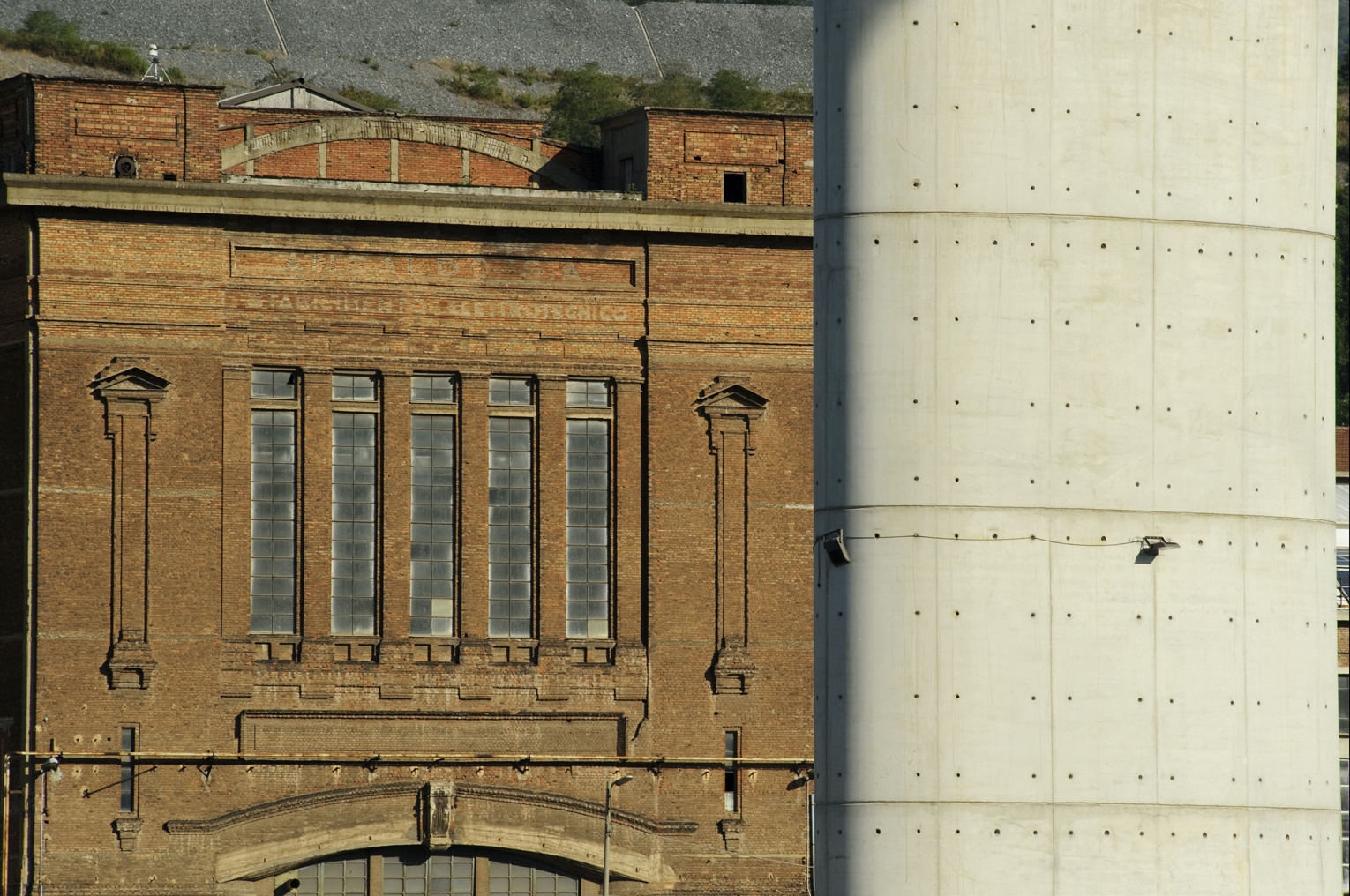
Il ruolo dell’università
La ricerca svolta presso il Centro CIRCe si basa sulla caratterizzazione e analisi multi-scala dei materiali cementizi e lo studio delle loro applicazioni. «Le proprietà macroscopiche dei materiali cementizi che utilizziamo nella realizzazione di un’opera, come la possibilità di erigere dei piloni in tempi brevi con proprietà ingegneristiche adeguate, – spiega il prof. Artioli – in realtà si basano sulla microstruttura e sulle proprietà chimico-fisiche dei materiali. La collaborazione con l’università consente di ottenere un livello di conoscenza e di comprensione dei materiali che normalmente l’industria non è in grado di conseguire perché necessita di competenze e strumentazioni avanzate, incluse le grosse sorgenti di radiazione, per esempio luce di sincrotrone o fasci neutronici, normalmente di difficile accesso per la maggior parte delle realtà industriali italiane. Sorgenti estremamente intense di questo tipo riescono a penetrare all’interno del materiale, e a seguire il materiale nella sua evoluzione a livello atomico-molecolare». Il Centro fornisce quindi all’industria una “expertise” nell’utilizzo e nel disegno di questi esperimenti non facile da ottenere in un normale laboratorio di R&S. «Questo ha permesso di sviluppare e ottimizzare dei prodotti nuovi, come nel caso degli acceleranti utilizzati nel ponte» precisa Artioli. «Si tratta di una collaborazione alla pari perché l’industria ha quelle potenzialità di scala sui materiali che l’università non ha nei propri laboratori, con prospettive applicative molto diverse rispetto a quelle della ricerca fondamentale. La collaborazione stretta consente di giungere a un percorso ottimale, sia a livello delle proprietà dei materiali che nell’economia di scala del processo. Nel caso di questa nuova generazione di additivi, è stata una piacevole sorpresa vedere confermati alla grande scala gli effetti precedentemente osservati in laboratorio, sia in termini di accelerazione del processo che di modifica della microstruttura e quindi di una più lunga durabilità». A partire dai risultati ottenuti sul ponte di Genova San Giorgio, gli sviluppi futuri della ricerca sono riposti nella comprensione dei meccanismi di reazione in formulazioni innovative e nell’ottimizzazione di nuovi additivi altrettanto promettenti, applicabili in futuro ad una più ampia varietà di cementi.
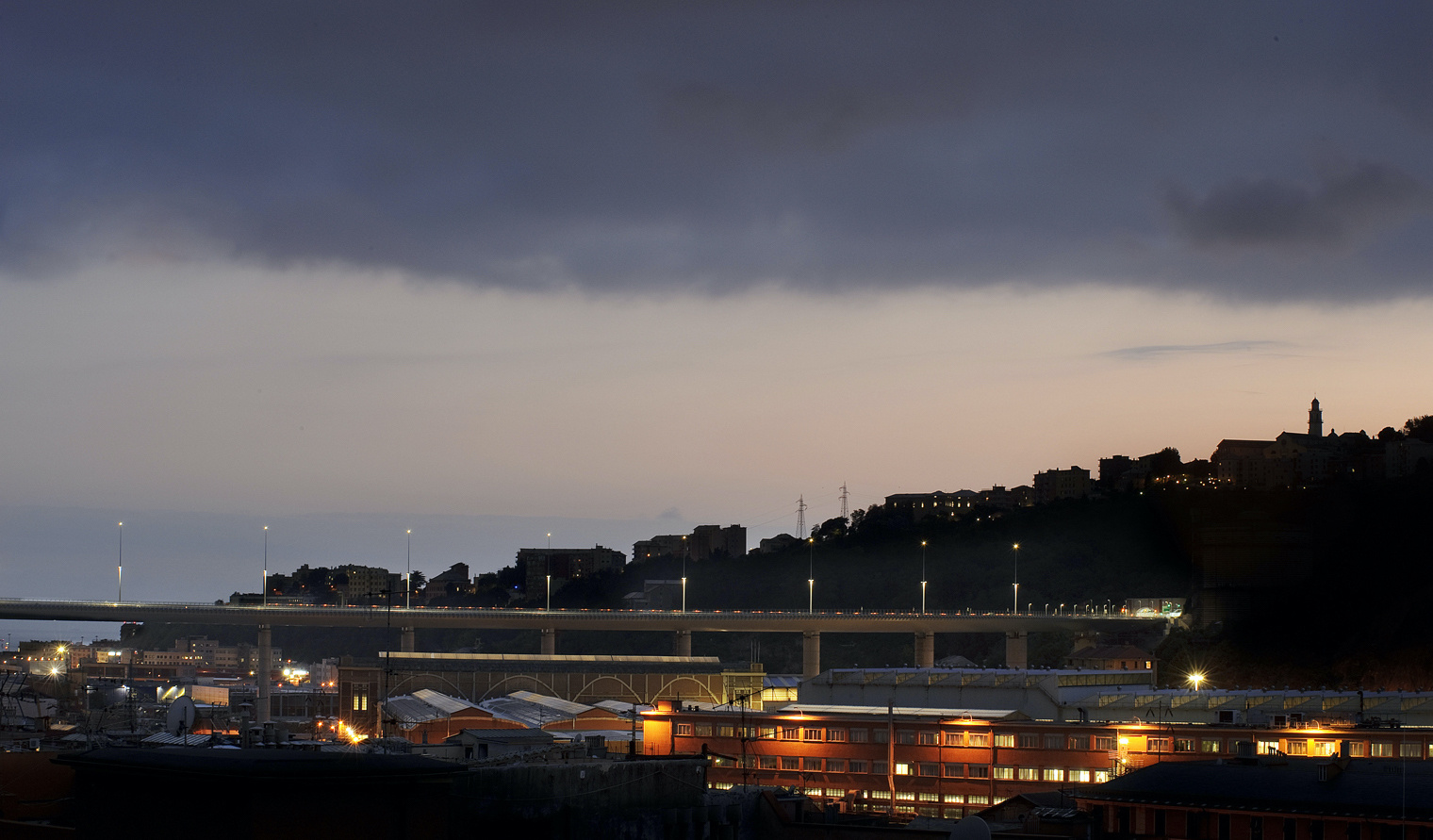
In conclusione, due sono gli insegnamenti che possiamo trarre dalla ricostruzione del Ponte. Fondamentali, per il successo dell’impresa, sono state la collaborazione con la filiera e con il mondo dell’Università. La sinergia tra quest’ultimo e due imprese leader del settore delle costruzioni è una testimonianza importante di come la ricerca applicata possa rappresentare un vantaggio per tutta la filiera. Inoltre, è proprio grazie ad un gioco di squadra che ha coinvolto tutta la filiera delle costruzioni che è stato possibile vincere la sfida della ricostruzione. Il modello adottato, nell’approccio multidisciplinare di progetto e nella sinergia continua tra i protagonisti della filiera, ha rimarcato la centralità del dialogo e del confronto tra committenza, progettisti e fornitori, partner nella realizzazione dell’opera, quali elementi di successo per il superamento delle problematiche di cantiere.
Un modello auspicabilmente replicabile anche in futuro e alla base di un nuovo modo di costruire, in cui proprio il dialogo tra tutti i protagonisti della filiera delle costruzioni diventa garanzia di corretta progettazione, corretto ingaggio, corretta fornitura di materiali e quindi sinonimo di qualità, competenze, responsabilità, etica, trasparenza, al servizio di chi usufruirà dell’opera.
© RIPRODUZIONE RISERVATA